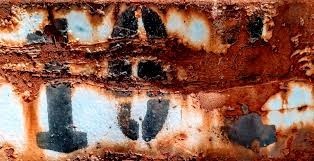
BIZ.VOM : la corrosion aqueuse des métaux zingués
Il est impossible de tout résumer lors d’une table ronde, c’est pourquoi nous avons abordé la corrosion des aciers revêtus de zinc et tenté d’expliquer l’avantage ou non d’ajouter d’autres éléments d’alliages comme l’aluminium ou le magnésium.
Autour de cette table ronde animée par Promosurf, étaient présents : Prof. Marjorie Olivier (UMONS), Grégory Guilbert (Materia Nova), Céline de Lame (NLMK), Bruno Bertrand (Chemetall), Sébastien Le Craz (CRMGroup).
La corrosion métallique est un phénomène qui existe depuis que les hommes ont réussi à préparer des métaux qui ne se trouvaient pas naturellement à l’état métallique.
La corrosion est le phénomène suivant lequel les métaux et les alliages métalliques subissent de la part de leur environnement, quel qu’il soit, une attaque dont la conséquence est de les faire retourner vers leur forme stable oxydée.
La corrosion consiste en l’oxydation des métaux et la réduction d’un agent oxydant présent dans le milieu corrosif.
Le phénomène de corrosion met donc en jeu des réactions d’oxydo-réduction. La corrosion est un processus anodique. Les métaux courants tels que l’aluminium, le zinc et le fer s’oxydent en milieux aqueux. Les électrons produits sont consommés par la réaction cathodique (de réduction) qui suivant le pH et l’aération donneront lieu à la réduction de l’eau, des protons ou de l’oxygène dissous.
A l’anode :
Al→Al3+ +3e-
Fe→Fe2+ +2e-
Zn →Zn2+ + 2 e-
A la cathode :
2H2O+2e- →H2 +2OH-
2H+2e-→H2
O2 + 4e- + 4H+ → 2H2O
Afin de garantir une protection de l’acier contre la corrosion, différents alliages de zinc peuvent être utilisés, chaque alliage ayant des avantages et des inconvénients. En cas de griffe, l’acier plus noble que le zinc est le siège de la réaction cathodique et reste intact tandis que le zinc s’oxyde, se corrode, se sacrifie pour protéger l’acier. Sa fonction est donc de s’oxyder en lieu et place de l’acier en cas de couplage galvanique.
Afin de retarder la corrosion du revêtement de zinc, différents métaux sont ajoutés dans les bains de zinc. Ceux-ci sont connus pour leur pouvoir réducteur plus important. Les couches de zinc alliées avec de l’aluminium et du magnésium ont montré une meilleure protection contre la corrosion en corrosion atmosphérique.
La corrosion est un processus complexe qui dépend principalement des conditions d’exposition du substrat. Différents types de produits de corrosion sont formés à la surface de la couche de zinc en fonction de son exposition : immersion dans une solution aqueuse ou exposition à l’air.
Nous allons surtout parler de la corrosion atmosphérique des métaux zingués. L’électrolyte dans ces conditions vient de la condensation et des pluies. La pollution étant un facteur accélérant la corrosion. On trouve donc dans l’eau des éléments comme le dioxyde de carbone (CO2), de l’azote et ses dérivés (nitrates /nitrites), du souffre (sulfates), etc…
Ces couches de zinc se corrodent environ 100 fois moins vite que l’acier grâce à leur pouvoir « barrière » provenant de la formation de produits insolubles barrière après oxydation. Près des côtes, le long de la mer, la présence de chlorure accélère la dissolution des couches de zinc (Tableau 1) par rapport au milieu rural.
Estimation de la perte en masse de zinc en fonction des conditions d’exposition.
Tableau 1 - Zinc consumption (in μm/year) as a function of the exposure environment57(source UMons: J.Rodriguez)
Tous les alliages de zinc sont déposés en majorité par électrodéposition ou par immersion dans un bain à chaud. Les marchés utilisant ce type de revêtements sont nombreux : automobile, bâtiments, électro-ménager, etc.
Après l’immersion de l’acier dans le bain de zinc à chaud, il se forme une couche de protection de zinc adhérant d’épaisseurs variables en fonction de la protection souhaitée.
La couche formée, en fonction de sa qualité, est donc composée de zinc et d’intermétalliques zinc-fer ou autres si le bain de zinc contient de l’Al et/ou du Mg. La complexité des microstructures est ici un paramètre essentiel pour comprendre les mécanismes de corrosion.
L'amélioration de la protection sacrificielle de l'acier offerte par les revêtements de zinc est d'un grand intérêt depuis de nombreuses années. Des revêtements de zinc alliés avec Al, Mg ou une combinaison des deux, ayant montré une résistance à la corrosion améliorée par rapport à la galvanisation classique, ont donc été développés. Les différents types d'alliages répertoriés dans la littérature sont repris dans le tableau 2. Les mécanismes de corrosion de ces alliages sont développés en se concentrant sur l'influence du magnésium.
Tableau 2- Zn-Mg-Al coated steel commercialized between 1985 and 2010 and their corresponding composition in Zn, Mg and Al (in wt. %)53 (source UMons: J. Rodriguez)
Les revêtements de Zn-Mg-Al obtenus par immersion à chaud sont composés de trois phases principales : une phase riche en Zn, une phase riche en Al et la phase intermétallique MgZn2. Ils peuvent être trouvés sous la forme de l'eutectique binaire MgZn2-Zn, de l'eutectique binaire Zn-Al et / ou de l'eutectique ternaire Zn-Al-MgZn2 selon la composition du revêtement.
Cette microstructure complexe est un paramètre crucial pour la compréhension des mécanismes de corrosion.
Exemple d’une couche de Zn/Al/Mg.
Mise en Peinture des substrats zingués
Après application de la couche de zinc, les substrats peuvent être peints soit dans les ateliers intégrés, post-peinture, soit en continu par défilement, dans les lignes de coil-coating.
Avant l’application d’une peinture, les substrats doivent subir une désoxydation afin de garantir une bonne réactivité de la couche de conversion et des polymères présents dans les peintures. Cette couche d’oxydes est présente sur tous les supports et est la résultante du refroidissement du zinc à l’air ambiant.
La mise en peinture et le choix des peintures seront abordés dans un autre article du VOM Info.
Promosurf remercie tous les participants à cette table ronde et plus particulièrement Prof. M. Olivier et J. Rodriguez pour les renseignements reçus.
Cet article est paru dans le VOMinfo d'août 2020, édition 04/2020