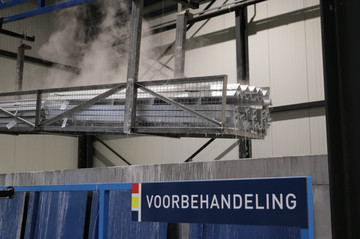
Seaside class, Qualimarine, Preanodisatie, 2-laags poedercoating…. wat betekent het?
Filiforme corrosie: legeringsonderzoek
We gaan even een kleine 20-tal jaren terug, toen er nog volop werd gediscussieerd over de oorzaken van het ontstaan van filiforme corrosie op gepoederlakte aluminium bouwdelen. Onder impuls van de looncoaters op aluminium heeft er destijds een onderzoek plaats gevonden geleid door professor metallurgie J. Defrancq, die de invloed van de diverse legeringselementen in het aluminium, op het ontstaan van filiforme corrosie heeft onderzocht. Uit het resultaat van deze studie bleek dat er vanaf bepaalde concentraties koper, ijzer, zink en nog enkele andere voorkomende legeringselementen in marktconforme extrusielegeringen, een negatieve invloed ontstond op het eventueel ontstaan van corrosie. Naar aanleiding van de resultaten van dit onderzoek is dan de term ontstaan: ”De zgn. S2 legering” als zijnde een “superieure” legering die het ontstaan van filiforme corrosie zou minimaliseren.
In de daaropvolgende jaren heeft men dan, tevergeefs, getracht om de extrudeur te overtuigen om hun productieprocessen zodanig aan te passen om de grenswaarden van deze legeringselementen wat nauwer te maken. De problematiek werd echter al gauw doorgeschoven naar de oppervlaktebehandelaar die dan uiteindelijk de conclusie trok: hoe dieper men kon afbeitsen, hoe meer “schadelijke” legeringselementen men zou verwijderen.
Seaside class
Het ontstaan van de Seaside-class voorbehandeling was een feit. De huidig specificaties in de Qualicoat - richtlijnen spreken nu van een “standaard” beitsafdracht van 1 g/m² en een “seaside” beitsafdracht van 2 g/m². De term “Seaside” komt dan van de aanbeveling om dieper te beitsen wanneer de betreffende aluminium bouwdelen worden geplaatst in agressievere milieus zoals bijvoorbeeld de kustlijn.
Deze maatregel en nog een aantal andere maatregelen hebben effectief geleid tot minder corrosie-gevallen in de afgelopen jaren. Er is dus wel degelijk een verbetering waarneembaar geweest. In hoeverre dit dan te wijten was aan de beitsafdracht of aan een aantal andere verbeteringen zoals bijvoorbeeld de afrondingsstraal van aluminiumprofielen, is uiteraard niet wetenschappelijk bewezen. Maar algemeen kan men wel besluiten dat een “diepere beits” zeker zijn nut heeft en een verbeterde corrosieweerstand tot gevolg heeft.
Gelijklopend met deze ontwikkelingen zijn er een aantal “neveneffecten” ontstaan in het marktsegment. Zo ontstond de discussie of de vastgelegde 2 g/m² nu al dan niet moest worden gebeitst in zuur en/of alkalisch milieu en dan nog eens in 1 of in 2 fasen. In Frankrijk (en ook daar alleen) was men overtuigd dat dit moest gebeuren in een alkalische beits gevolgd door een zure beits. Omdat de rest van Europa niet echt deelde in die mening is er dan nog eens een klasse apart ontstaan, nl. de Qualimarine classificatie!
Samengevat hebben we nu in de officiële Qualicoat specificaties de volgende classificaties:
Seaside beitsafdracht:
- Type A (acid etching): Type A1 = simple acid etching
- Type A2 = acid etching + acid etching
- Type AA (dual etching): Type AA1 = alkaline etching and acid etching
- Type AA2 = acid etching + alkaline etching + acid etching.
Onze mening: 2g is 2g!! Ongeacht op welke wijze deze beitsafdracht wordt bekomen. Wij zien geen enkel verschil in de wijze waarop men 2 g/m² afbeitst. Het is bijvoorbeeld niet bewezen dat een zoutsproeitest op een AA stuk altijd een beter resultaat zou opleveren dan bij een A stuk. Daarnaast dragen we nog eens bij aan het beperken van onze afvalstromen. De combinatie van alkalisch beitsen gevolgd door zuur beitsen geeft nl. meer slib-afval dan het enkelvoudige zure beits.
Pré-anodisatie
Gelijklopend is de discussie ontstaan over een anodisatielaag als conversie voorafgaand aan het poederlakken. Deze zgn. préanodisatie zou dan gelijkwaardig zijn aan een seaside klasse. Het is bewezen dat een uitmuntend uitgevoerde préanodisatie inderdaad ook een goede conversielaag is voor het poedercoaten. Concreet betekent dit een anodisatielaag van ca. 5 µm laagdikte, die onder nauwkeurige, specifieke procesparameters dient aangebracht te worden. Aansluitend moet er zeer goed gespoeld worden om alle zuurresten uit de poriën te kunnen verwijderen. Vervolgens dient de poedercoating binnen de 24 uren aangebracht te worden om te vermijden dat deze poriën aangetast worden door oxidatie. In de praktijk betekent dit dat het anodiseren en poederlakken in feite onder één dak dient te gebeuren.
Onze mening: Pré anodiseren is een evenwaardig alternatief voor een diepere beitsafdracht maar is ingewikkelder en gevoeliger in uitvoering. Het spreekt voor zich dat het daarom een hogere kostprijs heeft o.a. door de langere doorlooptijd en het hogere energieverbruik van een anodiseerproces.
1-laags of 2-laags poedercoaten
Als laatste willen we nog de discussie omrent een 2-laagsysteem onder de loep nemen. Bij “normale” omstandigheden geeft een standaard laagdikte tussen 50 – 70 µm voldoende bescherming tegen corrosie. In bepaalde gevallen is het toepassen van hogere laagdikten aan te bevelen. De kantendekking op “scherpe” randen van de te coaten stukken speelt hier een belangrijke rol. Bij een standaard laagdikte van ca. 60 µm zal op de scherpe randjes hooguit 10 à 20 µm overblijven. Het spreekt voor zich dat dit dan een zwakke plek blijft t.a.v. het ontstaan van corrosie.
Vandaar dat men in extreme situaties vaak opteert voor een 2-laagssysteem om op deze scherpe randen toch nog minstens 60 µm over te houden. De zgn. afrondingsstraal van profielen speelt hier uiteraard ook een grote rol. Hoe meer de randen afgerond worden, hoe eenvoudiger het is om op deze randen ook een optimale laagdikte te bekomen, zelfs in één laag. M.a.w. bij voldoende afronding is een hogere laagdikte niet echt nodig. Anderzijds zou men logischerwijs kunnen stellen dat een hogere laagdikte uiteraard langer weerstand biedt aan aantasting door agressieve atmosferische omstandigheden. Daarom zou men kunnen opteren om bij deze situaties de standaard laagdikte van 60 µm bijvoorbeeld te verhogen naar 90 µm. Gekende agressieve omstandigheden zijn: kustlijn (zoutneerslag), zwembaden (chloriden), trein-tram verkeer (ijzer-koperdeeltjes), zware industriële uitstoot (chemicaliën), langs de straat (vb. strooizout), …. Uiteraard is dit geen limitatieve opsomming. In bepaalde agressieve omstandigheden of bij stukken met veel scherpe randen is een verhoogde laagdikte aan te bevelen.
Conclusie
Al het voorgaande in acht genomen heeft Maes Coating Service het aanbrengen van een poedercoating onderverdeeld in 3 classificaties:
- Standaard: seaside chemische voorbehandeling + 60 µm laagdikte
- Laagdikteklasse 1: seaside chemische voorbehandeling + 90 µm laagdikte in één laag.
- Laagdikteklasse 2: seaside chemische voorbehandeling + 100 à 120 µm laagdikte in 2 lagen.
Merk op dat wij ALTIJD de SEASIDE-voorbehandeling zullen toepassen omdat wij van mening zijn dat dit de grootste positieve invloed heeft op een kwalitatief eindproduct. Zeker nu er de laatste jaren meer en meer aluminium op de markt komt waarvan de oorsprong voor de looncoater niet gekend is. Ook het toenemend gebruik van gerecycleerd aluminium speelt hierbij een rol. Vandaar dat wij ervan uit gaan dat de kans op een te hoge concentratie aan “schadelijke” legeringselementen in het hedendaags aanbod van aluminium producten ook aanzienlijk is geworden. Een “diepere” beits verdient daarom zeker een aanbeveling!
Dit alles in het kader van een optimaal grondstoffenbeheer. We staan voor een vaststaand feit dat aluminium als grondstof in de komende jaren toch “verontreinigd” gaat worden door de toenemende integratie van recyclage. Tegelijkertijd trachten wij het verbruik van chemicaliën (A1-beits) en poedercoatings (laagdikte) zo efficiënt mogelijk te optimaliseren.
Meer informatie: Ludo Appels, Compri Coating Service. De gegevens vindt u op de ledenpagina van VOM.
Dit artikel is gepubliceerd in VOMinfo april 2020, editie 02/2020.