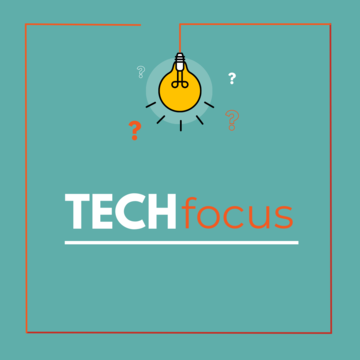
CAMPAGNE TECHfocus : REVÊTEMENTS MÉTALLIQUES
Dans ce TECHfocus, nous mettons en lumière les procédés qui permettent d'appliquer un revêtement métallique sur un substrat. Par souci de clarté, nous présentons 6 techniques d'application de revêtements métalliques :
1. Procédés électrolytiques
2. Procédés sans courant
3. Pulvérisation thermique / Métallisation
4. Immersion dans un bain de métal en fusion
5. Dépôt sous vide
6. Pulvérisation/brossage
Procédés électrolytiques
Toutes les applications dans lesquelles une couche métallique adhésive est appliquée sur un substrat à l'aide d'un courant électrique relèvent du processus électrolytique. Ce procédé est également appelé galvanoplastie.
QUEL EST L'OBJECTIF ?
L'application d'une couche métallique très fine par le biais du processus électrolytique vise à modifier les propriétés de la surface. Les propriétés les plus courantes sont : l'aspect décoratif, l'amélioration de la résistance à la corrosion ou les propriétés techniques telles que la résistance à l'usure, l'adhérence, les propriétés de glissement, etc.
PRINCIPE ?
L'électrolyse se produit lorsqu'un courant électrique traverse un liquide contenant des ions. En général, l'électrodéposition est réalisée dans un bain contenant un liquide galvanique, appelé bain galvanique. La solution aqueuse (=électrolyte) contient principalement des sels, des acides, des bases ou diverses combinaisons de ceux-ci.
Dans ce bain, vous avez une (des) tige(s) anodique(s) du métal à appliquer (chargée(s) positivement) et une tige cathodique (chargée négativement) où votre pièce à usiner est suspendue. Les ions chargés négativement se déplacent vers l'anode (=anions) et les ions chargés positivement se déplacent vers la cathode (=cations). Ceux-ci sont connectés à leur pôle positif ou négatif respectif d'une source de courant continu.
Lorsque le courant passe, il y a précipitation de métal et/ou dégagement d'hydrogène à la cathode et dissolution de métal et/ou dégagement d'oxygène à l'anode.
La quantité de métal précipité par un courant électrique est déterminée par l'intensité du courant, la durée de l'électrolyse et l'équivalent électrochimique du métal en question.
APPLICATIONS
La technologie de galvanisation existe sous de nombreuses variantes en fonction du métal déposé. Les plus connues sont le chromage décoratif (p. ex, la robinetterie dans les applications sanitaires), le chrome dur (p. ex, l'industrie textile, les tiges), la galvanisation (p. ex, les fixations), la dorure (p. ex, les semi-conducteurs, décoratifs), le nickelage (p. ex les pièces anciennes), l'argenture (p. ex, la bijouterie).
Dans une usine de galvanoplastie, on trouve souvent une série séquentielle de bains car le revêtement final est composé de plusieurs couches. Un exemple est le nickel duplex où deux couches de nickel sont appliquées. Un autre exemple est le chromage qui est appliqué comme touche finale après le nickelage.
Il existe également différents degrés de finition : de mat, brillant à très brillant (effet miroir).
L'épaisseur de la couche des revêtements électrolytiques varie en fonction de l'application. Elle est généralement comprise entre 5 et 30 µm. Pour le chrome dur, elle peut atteindre 50 µm.
La galvanoplastie est un véritable travail d'artisan qui nécessite des connaissances et de l'expérience. De nos jours, les litiges et l'utilisation de produits chimiques sont strictement réglementés par les réglementations régionales et REACh. Il existe également de fortes fluctuations de prix en raison de l'économie mondiale et de l'accès à des métaux rares tels que l'or et le nickel.
Si vous souhaitez obtenir de plus amples informations ou vous entretenir avec un expert, veuillez contacter les membres suivants de la VOM :
Entreprises proposant une technologie de galvanoplastie
Fournisseurs de produits chimiques de base
Procédés sans courant
Outre le procédé électrolytique, il est également possible d'appliquer un revêtement métallique sur une surface par voie électrique. Le procédé le plus connu est le nickelage sans courant. Dans l'industrie des circuits imprimés, on utilise le cuivrage chimique. Cette technologie n'est toutefois plus utilisée dans les pays du Benelux. Nous nous limiterons donc à parler du nickelage chimique.
QUEL EST L'OBJECTIF ?
Le nickelage chimique est un procédé qui consiste à appliquer une fine couche de nickel sur une surface métallique. Il s'agit généralement d'un alliage nickel-phosphore (9 à 12 % en poids) appliqué par un procédé chimique (sans courant) par immersion dans un environnement aqueux. Il confère de nouvelles propriétés aux surfaces traitées et est utilisé, entre autres, pour améliorer la résistance à la corrosion et à l'usure des pièces métalliques.
La principale différence avec le nickelage électrolytique est que l'épaisseur de la couche est régulière et réglable avec précision, sans effet de bord.
PRINCIPE ?
Le processus de dépôt par voie "chimique" commence par l'immersion des objets dans des bains de prétraitement (Dégraissant/ Décapant). Cela permet d'obtenir un dépôt de haute qualité avec une adhérence moléculaire très stable sur le substrat. Les pièces sont ensuite immergées dans une solution de sels de nickel, de réducteurs et d'additifs (acides/complexants/tensioactifs...). La séparation des métaux se fait généralement par un processus autocatalytique. Ce processus est suivi d'un post-traitement. En option, un traitement thermique peut être effectué.
APPLICATION
Le revêtement étant dimensionnellement stable, il est souvent utilisé pour des pièces complexes à géométrie variable. Exemples : engrenages, tuyauterie, échangeurs de chaleur, pièces PEM, distribution de gaz.
Les principaux matériaux traités sont les aciers de construction, les aciers alliés, les aciers inoxydables, la fonte, l'aluminium et les alliages de cuivre.
L'épaisseur de la couche est fonction de la résistance à la corrosion requise (de 1 à 100 µm). Les taux de précipitation sont compris entre 10 et 15 µm/heure.
Le nickel chimique est très prometteur sur le marché de l'hydrogène pour la production d'énergie renouvelable.
Si vous souhaitez obtenir de plus amples informations ou vous entretenir avec un expert, veuillez contacter les membres suivants de la VOM :
Entreprises spécialisées dans le nickelage chimique
Fournisseurs de produits chimiques de base
Pulvérisation thermique/métallisation
La projection thermique fait référence à un groupe de techniques qui fusionnent un fil ou un matériau en poudre en ajoutant de la chaleur (énergie thermique), après quoi les gouttelettes formées sont accélérées par un flux de gaz et frappent le substrat à grande vitesse (énergie cinétique).
Nous pouvons diviser cette technologie en deux groupes :
· Métallisation
· Pulvérisation à haute fréquence
1. Métallisation
QUEL EST L'OBJECTIF ? La principale application de la projection thermique est la projection de zinc ou d'alliage zinc/aluminium pour la protection contre la corrosion, souvent appelée métallisation. L'aluminium est également utilisé à cette fin, ce que l'on appelle le procédé TSA.
PRINCIPE ?
Dans la métallisation au pistolet à gaz, un fil de zinc ou d'alliage de zinc-aluminium est introduit dans un pistolet à gaz alimenté en gaz (propane ou acétylène et oxygène). La combustion du gaz fait fondre le fil lors de son passage. Celui-ci est ensuite projeté avec de l'air comprimé sur la surface à métalliser.
Dans la métallisation à l'arc électrique, deux fils de zinc ou d'un alliage de zinc et d'aluminium sont introduits dans un pistolet de métallisation électrique. Lorsque les deux fils entrent en contact, un arc électrique se forme et fait fondre le zinc. Celui-ci est ensuite projeté par air comprimé sur la surface à métalliser.
Il convient de noter que l'application d'une couche de finition organique (revêtement en poudre ou peinture humide) est nécessaire en raison de la porosité élevée associée à la pulvérisation de zinc. Il est également important de contrôler minutieusement le processus, en particulier la température et les niveaux d'humidité, ainsi que le temps écoulé entre la pulvérisation et l'application de la couche de finition organique.
APPLICATION
Dans le domaine de la métallisation, il n'y a pas de limite à la taille ou au poids des structures à traiter. Bâtiments, ponts, moulins à vent, portes d'écluses, rien n'est trop grand ou trop lourd pour être métallisé. L'épaisseur de la couche de métallisation peut également être adaptée à la classe de corrosion. Les épaisseurs de couche varient généralement entre 50 µm et 200 µm.
La métallisation peut être réalisée en atelier ou sur site et est excellente pour traiter les structures trop grandes pour la galvanisation à chaud.
Des poussières et des vapeurs métalliques sont libérées dans l'air ambiant. Le port d'un équipement de protection individuelle est nécessaire, de même que l'aspiration et la ventilation des locaux dans les cabines de sablage.
2. Pulvérisation thermique HVOF
QUEL EST L'OBJECTIF ?
Une deuxième application importante est l'application de revêtements durs et résistants à l'abrasion, tandis que la réparation de pièces de machines usées, souvent avec des revêtements plus résistants à l'abrasion que le matériau d'origine, est également importante.
PRINCIPE ?
La projection thermique HVOF applique des couches résistantes à la corrosion et à l'usure d'une épaisseur allant de quelques microns à quelques millimètres. Le matériau est injecté sous forme de poudre dans un pistolet HP-HVOF spécial, après quoi il forme une couche extrêmement homogène présentant une grande force d'adhérence et une porosité minimale.
APPLICATION
Différents substrats, tels que le bronze, l'acier, l'aluminium, l'acier inoxydable et même les matières plastiques, peuvent être revêtus. Des couches combinées sont également appliquées, y compris, par exemple, des couches extrêmement résistantes à l'usure sur des couches résistantes à la corrosion. Ou encore des combinaisons de couches pulvérisées et d'une couche galvanique.
L'épaisseur de la couche dépend du type de revêtement : 25-5 000 µm
Les applications HVOF se retrouvent dans l'aviation (par exemple, les trains d'atterrissage), les centrales électriques (joints), la navigation (turbines), etc.
Si vous souhaitez obtenir de plus amples informations ou vous entretenir avec un expert, veuillez contacter les membres suivants de la VOM :
Entreprises spécialisées dans la métallisation
Entreprises spécialisées dans la pulvérisation HVOF
Fournisseurs de poudres métalliques
Fournisseurs d'équipements de pulvérisation thermique
Immersion dans un bain de métal en fusion
Après avoir plongé la pièce dans un métal en fusion, une couche de ce métal se forme sur le substrat. Le procédé le plus connu est la galvanisation à chaud, ou galvanisation dans le langage courant. Nous ne parlerons donc que de cette application.
QUEL EST L'OBJECTIF ?
La galvanisation à chaud est utilisée pour appliquer un revêtement épais, bien adhérent et bien corrosif (couche de galvanisation) sur des objets ou des structures en acier. La galvanisation à chaud peut être réalisée en continu, en discontinu ou en centrifugeuse.
PRINCIPE ?
Galvanisation à chaud discontinue
La galvanisation à chaud est un procédé de trempage dans lequel les objets sont immergés dans du zinc liquide à une température comprise entre 445 et 465°C pendant une courte période. Au cours de ce processus, des couches d'alliages zinc-fer se forment sur la surface du fer ou de l'acier, recouvertes d'une couche de zinc. L'épaisseur combinée des couches est généralement comprise entre 50 et 150 µm.
Galvanisation à chaud en continu
Dans la galvanisation à chaud en continu, la bande ou le fil d'acier est galvanisé en continu après des recuits d'oxydation et de réduction successifs, ce qui permet d'obtenir des couches de zinc d'une épaisseur de 15 à 30 µm. Le matériau galvanisé est ensuite traité. Pour les bobines, les tôles, etc. galvanisées en continu, le commerce spécifie le poids de la couche de zinc par m² de surface double face, contrairement à ce qui est habituel pour les objets galvanisés de manière discontinue. Dans la pratique, le poids de la couche de zinc sur les deux faces se situe entre 200 et 450 g/m².
Galvanisation par centrifugeuse
La galvanisation par centrifugation est également un procédé de galvanisation à chaud. Après avoir été prétraités, les matériaux sont galvanisés dans des paniers. Lorsque les paniers sortent du bain de zinc, ils sont placés dans une centrifugeuse. Cette centrifugeuse évacue le zinc qui n'a pas réagi. L'épaisseur de la couche de zinc obtenue est donc légèrement inférieure à celle de la galvanisation à chaud discontinue.
Seules les petites pièces telles que les boulons, les écrous, les goujons, les plaques d'esquisse, etc. peuvent être galvanisées à chaud de cette manière.
APPLICATION
On trouve des pièces galvanisées à chaud aussi bien dans le paysage urbain que le long des autoroutes, dans des environnements industriels et ruraux. Pensez aux glissières de sécurité, aux clôtures industrielles, aux escaliers, au mobilier urbain, aux ponts, aux ouvrages d'art, etc.
La galvanisation à chaud discontinue présente le grand avantage de bien protéger les coins et les arêtes et de protéger les structures creuses à l'intérieur. Il convient toutefois de s'assurer que le substrat peut résister à l'échauffement qui se produit et que la conception de l'objet à galvaniser est telle qu'une couverture complète est possible.
C'est avant tout l'épaisseur de l'acier qui détermine l'épaisseur du revêtement de zinc. Les épaisseurs minimales d'acier requises sont fixées dans les normes de galvanisation. Toutefois, certains types d'acier donnent des résultats différents. Si la surface à galvaniser est plus rugueuse, l'interaction entre l'acier et le zinc en fusion est plus importante, ce qui entraîne des épaisseurs de couche plus importantes. Les petites pièces telles que les boulons, les écrous et les charnières subissent une galvanisation dite par centrifugation, ce qui permet d'obtenir des couches plus fines.
Si vous souhaitez obtenir de plus amples informations ou vous entretenir avec un expert, veuillez contacter les membres suivants de la VOM :
Entreprises spécialisées dans la galvanisation à chaud
Dépôt sous vide
QUEL EST L'OBJECTIF ?
Il existe différents procédés pour appliquer des métaux, des alliages, des composés métalliques et des non-métaux dans un vide plus ou moins poussé. Les noms de ces procédés se recoupent partiellement.
PRINCIPE ?
L'application de revêtements métalliques dans un environnement sous vide peut se faire de plusieurs manières :
· Évaporation : évaporation du métal à appliquer (évaporant) dans un vide à haute température, après quoi il précipite sur un substrat froid ou presque froid.
· Pulvérisation : Dans un vide pas trop poussé, un champ électrique de 1 à 5 kV provoque l'ionisation du gaz présent. Une décharge lumineuse est créée, les électrons (négatifs) se déplaçant vers l'anode et les ions positifs vers la cathode. Ces ions gazeux sont les ions de pulvérisation, qui bombardent la cathode, constituée du matériau à éroder.
· Placage ionique : Le chauffage du matériau à évaporer peut se faire de la même manière que l'évaporation, par chauffage par résistance, par chauffage par faisceau d'électrons et par chauffage à haute fréquence. En principe, tous les métaux peuvent être évaporés par placage ionique, qui peut également être évaporé sous vide. Il s'agit d'une technologie relativement nouvelle.
· Implantation ionique : elle consiste à bombarder un solide amorphe ou cristallisé avec des ions accélérés, en les introduisant dans la surface. Le processus se déroule sous vide, 1-0,01 Pa, avec des énergies très variables. L'épaisseur de la couche, qui est chimiquement modifiée par l'introduction d'ions étrangers, ne dépasse généralement pas quelques micromètres, mais pour certains substrats, la couche dont la composition est modifiée peut atteindre 100 à 200 μm.
· PVD, le dépôt physique en phase vapeur: il s'agit d'un processus réalisé sous vide poussé et, dans la plupart des cas, à des températures comprises entre 150 et 500 °C. Dans le processus PVD, le matériau de revêtement solide et très pur (métaux tels que le titane, le chrome et l'aluminium) est évaporé par la chaleur ou par bombardement d'ions (pulvérisation cathodique). Simultanément, un gaz réactif (par exemple de l'azote ou un gaz contenant du carbone) est ajouté. Ce gaz forme avec la vapeur métallique un composé qui se dépose sur les outils ou les pièces sous la forme d'un revêtement mince et très adhérent. Une épaisseur de revêtement uniforme est obtenue en faisant tourner les pièces autour de différents axes à une vitesse constante.
· CVD, dépôt chimique en phase vapeur : il s'agit d'un nom général pour un groupe de procédés qui peuvent être définis comme le dépôt d'un solide sur une surface chauffée par une réaction chimique pendant la phase vapeur. Températures typiques : 700 - 1000°C.
· PACVD, CVD assistée par plasma: L'installation de ce procédé est similaire à celle de la pulvérisation cathodique, qui est souvent utilisée en combinaison avec le dépôt en phase vapeur (CVD). Dans le PACVD, un gaz contenant les éléments du revêtement est introduit dans la chambre à vide et une décharge alimentée par une tension alternative est allumée.
APPLICATION
Les dépôts sous vide trouvent leur application dans les outils et les composants de précision qui requièrent une plus grande productivité, un frottement plus faible, une plus grande fiabilité et une durée de vie plus longue. Exemples : outils de coupe, pièces rotatives dans les moteurs et les machines, industrie électronique, revêtements décoratifs sur les stylos à plume, revêtements de type diamant DLC, etc.
Il y a beaucoup de nouvelles tendances et de désignations commerciales sur ce marché. Nous recommandons de bien s'informer sur les spécifications techniques de la technologie choisie.
Si vous souhaitez obtenir de plus amples informations ou vous entretenir avec un expert, veuillez contacter les membres suivants de la VOM :
Entreprises spécialisées dans la technologie du vide
Pulvérisation/brossage
QUEL EST L'OBJECTIF ? Application d'un revêtement métallique par pulvérisation ou au pinceau. Le plus connu est le revêtement métallique riche en zinc.
PRINCIPE ?
Il s'agit d'un système de galvanisation à film monocomposant contenant 96 % de zinc (poussière) dans le film sec. Le produit réagit immédiatement avec le substrat. Il peut être appliqué au pinceau, au rouleau ou au pistolet, sur des substrats propres ou rugueux, dans diverses conditions atmosphériques.
APPLICATION
Il peut être utilisé comme système de revêtement unique, comme primaire dans un système duplex (actif + passif) ou comme système de rechargement pour fournir une protection supplémentaire au produit. Applications : piliers de ponts, pylônes, bâtiments,...
Si vous souhaitez obtenir de plus amples informations ou vous entretenir avec un expert, veuillez contacter les membres suivants de la VOM :
Fournisseur de peintures métalliques
Vous êtes un expert dans ce domaine et votre entreprise ne figure pas dans la liste ? Contactez la VOM à l'adresse: info@vom.be