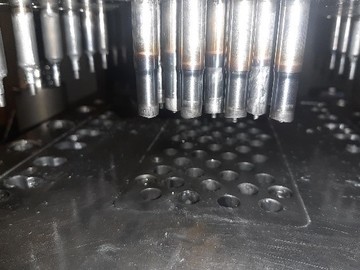
Résultats finaux du projet de recherche Cornet DCT4Cut
Le projet Cornet DCT4Cut consacré à la coupe et au poinçonnage a débuté en 2019 et s'est achevé au début de cette année. Après plus de deux ans de recherche, Sirris et VOM ont collaboré avec deux départements du célèbre Institut Fraunhofer en Allemagne : l'IST à Braunschweig et l'IWU à Chemnitz. Le projet a examiné les avantages de l'acier PM, les avantages du traitement cryogénique et de l’utilisation de revêtements spéciaux (PVD) sur la durée de vie des outils de poinçonnage complexes.
But de DCT4Cut
Ce projet de recherche comprend plusieurs lots d’activités consacrés à l'utilisation de l'acier pour travail à froid pour les applications de poinçonnage. Le terme « travail à froid » concerne l'application, à savoir les opérations telles que le poinçonnage, réalisées à température ambiante. Le nombre d'aciers de ce groupe est très élevée. C’est pourquoi nous les aborderons brièvement ci-dessous. En outre, le projet a tenté de démontrer les avantages d’un traitement thermique spécial : l’utilisation d’un traitement cryogénique (DCT constant - deep cryogenic treatment - et DCT cyclique), ainsi que l’utilisation de revêtements spéciaux (PVD) sur la durée de vie d’outils de poinçonnage complexes.
Pour cette étude, quatre types d'aciers différents pour travail à froid ont été sélectionnés : un acier conventionnel pour travail à froid K110 (1.2379), utilisé comme référence, un acier raffiné ESR Caldie et deux aciers pour métallurgie des poudres (PM) : Vanadis 4E et K390. Les aciers ESR et PM possèdent comme avantage principal une grande pureté de la structure à coeur (moins d’inclusions). De plus, les aciers PM possèdent une structure plus uniforme dans les trois directions (structure « isotrope »). Leur granulométrie est par conséquent plus fine, tout comme les carbures présents par rapport aux aciers ESR et aux aciers conventionnels fondus.Le choix de ces quatre aciers s’est basé sur l'expérience acquise dans le cadre du projet Infiblank et sur l'expérience de divers utilisateurs industriels en Belgique et à l'étranger. Il existe bien entendu de nombreuses autres sortes d’aciers qui peuvent être envisagées pour l'application visée. D’autres types d’aciers seront abordés dans la partie sur les tests industriels.
Les barres à partir desquelles le poinçonnage est réalisé ont été trempées dans un atelier de trempe à façon, où une méthode de durcissement conventionnelle dans un four à vide a été combinée à un traitement cryogénique. La trempe a été effectuée dans deux entreprises actives dans le secteur du refroidissement cryogénique industriel. La dureté visée était de 59+2 HRC.
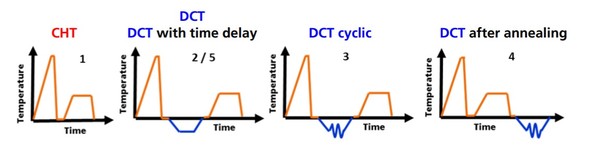
Figure 1 : différents cycles de trempe pour les essais
Stratégie d'essai
La figure 1 montre schématiquement les différentes possibilités afin de tremper l’acier pour travail à froid, avec ou sans utilisation d’un traitement cryogénique. Sur la gauche figure le cycle conventionnel, consistant en un traitement austénitique, suivi d’un traitement de revenu. Ceci dit, dans la pratique, on applique généralement un cycle de revenu triple. En outre, le deuxième graphique montre un cycle qui utilise un traitement cryogénique atteignant jusqu'à -196 °C directement après la trempe. Ce traitement est donc réalisé entre l’austénitisation et le revenu. Le troisième graphique montre une variante du traitement, consistant en un traitement cryogénique cyclique au cours duquel la température oscille entre -80 °C et -196 °C. Ce traitement cyclique est destiné à ramener à 8 heures la durée du traitement cryogénique constant (24 heures). Enfin, un « post-traitement cryogénique» est effectué. Le traitement cyclique est réalisé après le revenu, et donc à la fin du procédé de trempe. Le traitement cryogénique a comme but principal de réduire la présence d’austénite résiduelle formée lors de la trempe, augmentant ainsi la dureté et la stabilité dimensionnelle.
Selon la littérature, le traitement cryogénique serait également responsable d’une augmentation de carbures excrétés secondaires, ce qui augmente considérablement la résistance à l’usure. La diminution de la teneur en austénite résiduelle mentionnée n'a toutefois pas été constatée sur l’acier étudié, car un traitement de revenu triple lors d’un procédé de trempe est déjà responsable d’une diminution considérable de cette phase. L'augmentation apparente du nombre de carbures n'a pas non plus pu être confirmée expérimentalement. Enfin, les contraintes internes ont été provoquées par la trempe, mesurée avec et sans application d'un DCT. Cinq mesures ont été effectuées à l'aide d’un appareil de diffraction des rayons X mobile sur l’acier conventionnel, le K110, avec deux variantes DCT, dont un traitement cryogénique retardé, ainsi que sur l'acier PM K390. Aucune diminution ou augmentation significative des contraintes internes à la surface n'a été constatée pour K390, tandis qu’une seule légère augmentation a été constatée dans une direction pour KK110 (voir figure 2).
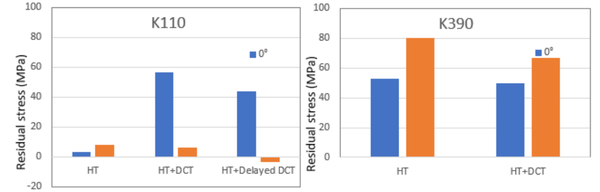
Essais en laboratoire
Une série de barres trempées a été envisagée selon les cycles ci-dessus et a ensuite été soigneusement caractérisée en termes de dureté, de structure, de teneur en carbure, de teneur en austénite résiduelle, de formation de fissures après un essai de rayure, etc. Ensuite, des poinçons ont été fabriqués à partir des barres au moyen d’électroérosion et testés en laboratoire par Fraunhofer IWU à Chemnitz. Une autre partie des barres a été envoyée au Fraunhofer IST à Braunschweig où elle a été recouverte de différents revêtements.
Essais sur les revêtements
Le Fraunhofer IST a surtout étudié l'influence de la stratégie de trempe : l'application du traitement cryogénique soit avant soit après le revenu et le revêtement (post-DCT). Les revêtements se composaient de couches PVD avancées, telles que WC-DLC et CrTiAlSiN, déposées avec et sans traitement préalable par nitruration plasma (PN). Ce dernier traitement n’est pas toujours réalisé, mais le poinçonnage a montré que l’adhérence et la résistance des revêtements augmentait, tout comme la résistance à l’écaillage des arêtes de coupe. L'influence du DCT réalisé avant la nitruration a donné peu de différence dans l'adhérence de la plupart des couches PVD, à la suite des essais de rayure. Le traitement de traitement cryogénique après l'application des revêtements TiAlSiN et CrAlTiSiN a toutefois établi une différence, à savoir une augmentation de la microdureté et du module de Young. Pour le poinçonnage, les revêtements CrAlTiSiN et WC ont été sélectionnés.
Résultat des essais en laboratoire
Pour assurer une différenciation suffisante, le choix s’est porté sur un poinçon (d’un diamètre de 5 mm) avec une forme partiellement angulaire et partiellement ronde. Le matériau à poinçonner était un acier inoxydable d’une épaisseur de 0,6 mm. La course était de 2 mm.
Ces poinçons ont permis de comparer les quatre matériaux tant en situation de trempée classique qu’en situation de trempée et de traitement cryogénique et sans revêtement. Dans l'état trempé conventionnel, on a constaté que le Vanadis 4E et le K390 donnaient le moins d'usure aux angles des poinçons. Après un traitement cryogénique, une usure moindre de l'arête de coupe (angle) a pu être constatée visuellement sur l'acier conventionnel K110 et sur Caldie. Les poinçons avaient alors effectué plus de 100.000 frappes.
Ensuite, de nouveaux poinçons ont été trempés et soumis à un DCT réalisé par une firme autrichienne. La température variait cycliquement entre -197 °C et -80 °C au lieu d'une température constante de -196°C. Après les essais de poinçonnage, on a observé, pour K110 et Caldie, comme dans le cas du DCT ordinaire, une réduction de l'usure, alors qu'aucune différence n'a été constatée dans le cas des aciers PM Vanadis 4E et K390.
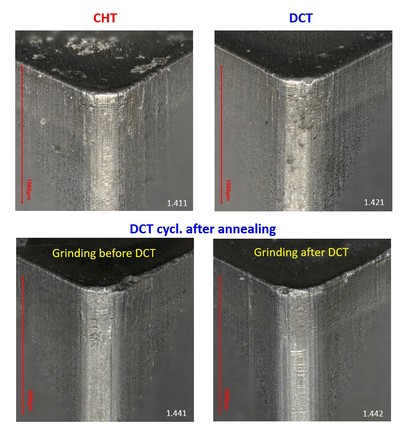
Figure 3 : Usure de l'angle de l’arête de coupe pour l’acier K390 et divers traitements
Enfin, des essais de poinçonnage ont été réalisés sur les quatre sortes d’aciers à l’aide de poinçons par traitement cryogénique cyclique et revêtus. Dans chaque cas, l'usure a été comparée à l'état sans revêtement. On a constaté que l'usure sur l'acier K110, trempé avec DCT et avec un revêtement CrTiAlSiN pourvu d’une couche de nitruration plasma sous-jacente était quasiment absente. Un résultat similaire a été obtenu avec l'acier ESR Caldie, ainsi qu'avec les autres aciers qui se sont également bien comportés sans revêtement.
Afin de vérifier l'effet de la nitruration plasma, une comparaison a été faite entre des poinçons trempés par traitement cryogénique et pourvus d'un revêtement en Vanadis 4E et en K390. L'adhérence du revêtement CrTiAlSiN s'est avérée tenir même sans PN, avec absence de toute forme d'usure aux angles des poinçons. Les revêtements (nitriques) riches en azote semblent d’un point de vue global fournir de meilleurs résultats que le WC et le DLC.
Résultat des essais industriels
L’étape finale du projet a consisté en divers essais industriels réalisés dans les deux pays. Ceux-ci sont destinés à transférer dans la pratique l'expérience acquise en laboratoire. Sirris a commencé ses essais industriels dans trois entreprises flamandes actives dans le poinçonnage de pièces en acier, telles que des rondelles, des profilés et des rivets. Les essais ont été effectués respectivement sur de l'acier K110 sans revêtement, du CPM4V, un acier PM américain, mais d’une composition proche de celle de Caldie et pourvu d’un revêtement duplex nitrique. Enfin, des poinçons en ASP23 sans revêtement ont été testés pour produire des rivets.
Figure 4 : Exemple de poinçons industriels utilisés pour les essais d’usure
Deux essais ont été exécutés avec des poinçons trempés avec traitement cryogénique et un revenu finale à haute température pour obtenir une dureté nominale d'environ 60 HRC. Lors du dernier essai, étant donné que les poinçons étaient déjà trempés, un seul traitement cryogénique a été appliqué à la fin et un traitement de revenu à basse température (post-DC) effectué afin de réduire les contraintes.
Lors du premier essai, une tôle d'acier en S235 d’une épaisseur de 8 mm a été utilisée afin de poinçonner des morceaux de tôle. Les poinçons ont été fabriqués à partir d’acier K110 conventionnel. Après environ 30.000 frappes, aucune différence claire n'a pu être établie entre les poinçons conventionnels et ceux avec traitement cryogénique. Les essais ont également été réalisés sur de l'acier haute résistance S700 d’une épaisseur de 1,5 mm. Ici, après environ 70.000 couches, on est parvenu à constater une amélioration, principalement dans l’écaillage des arêtes de coupe.
Un deuxième essai a été réalisé sur des poinçons en CPM4V, pourvus d’un revêtement duplex, pour le traitement d'acier CPM4V épais de 4 mm. Après environ 2.000.000 couches, on a comparé l’usure de deux moules équipés de plusieurs poinçons. Les poinçons avec traitement cryogénique ont nécessité un réaffûtage moins fréquent par rapport aux poinçons non traités par DCT.
Lors du dernier essai, qui a été réalisé sur des poinçons traités au post-DCT et avec de l'acier inoxydable comme matériau, une augmentation significative de la durée de vie a été constatée après environ 75.000-80.000 frappes. Une répétition de l'essai n'a toutefois pas indiqué la moindre augmentation, ce qui permet de conclure que le post-DCT a eu moins d’effet que le traitement DCT réalisé avant le revenu.
HSIC
En Allemagne, les essais industriels ont également été réalisés par diverses firmes qui, en plus de l'acier, ont aussi utilisé du plastique renforcé comme matériau de poinçonnage. Les essais réalisés sur du plastique semblaient néanmoins insuffisamment concluants. Ils ont donc été remplacés par des essais sur des tôles d'acier haute résistance pour la production de panneaux solaires. Déjà après 1.500 frappes, on a pu constater une usure moindre pour les poinçons fabriqués en K110 avec traitement cryogénique. De plus, des essais à poinçonnage ultra-rapide (abrégé en « HSIC ») ont aussi été réalisés. Les enseignements d'essais antérieurs chez IWU ont en effet montré que les poinçons HSIC dans les aciers pour travail à froid de haute qualité ont une durée de vie limitée en raison de la charge élevée pendant le poinçonnage. Pour les pièces traitées au DCT en S290 et en K105, la durée de vie pouvait être légèrement supérieure par rapport aux pièces trempées conventionnelles.
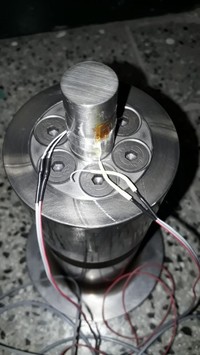
Figure 5 : Poinçon utilisé pour les essais HSIC.
Vue d’ensemble et conclusion
Le poinçonnage de l’acier, de l’inox et du plastique est un processus complexe au cours duquel de nombreux paramètres peuvent exercer une influence sur la durée de vie globale des outils de poinçonnage. Quelques paramètres importants sont le type d'acier pour travail à froid (conventionnel, EST ou PM), la dureté, la vitesse du poinçonnage, l’écart entre la tôle et le poinçon, l'état de la surface et la présence de revêtement ou de lubrification. En outre, la définition de la durée de vie dans les entreprises n’est pas toujours identique et dépend de différents facteurs. Par conséquent, il est très compliqué de tenir compte de tous ces paramètres et critères.
Cependant, on peut y tirer parti de l'application de DCT, éventuellement combinée à un revêtement. D’abord les aciers PM sont clairement supérieurs aux autres aciers indépendant de la méthode de trempe. Le traitement DCT a certainement du sens quand on utilise des aciers conventionnels pour atteindre des durées de vie considérables. Les avantages de la méthode se situe surtout au niveau de la réduction de l’usure abrasive (écaillage des bords). Si on envisage l’usure adhésive (grippage) l’utilisation des couches spéciales est recommandé. La combinaison des trois facteurs donnera une synergie afin que des matières à haute résistance à la traction et épaisseurs élevées peuvent être poinçonnées avec une longue durée de vie.
Le projet DCT4Cut est une initiative du Collective Research Network (CORNET) soutenu financièrement par AiF, FGW (Allemagne) et VLAIO (Flandre) et mené par Sirris, VOM et Fraunhofer IWU et IST.
Auteur artikel: Guy Claus
Contact : Bart.Teerlinck@sirris.be